UPCAST® Upgrades benefit customers in various ways
UPCAST OY carries out continuous development work. Thanks to the various upgrades, the UPCAST® products will remain up to date for decades
| TEXT: Sari Lommerse | PHOTOS: Maarit Hämäläinen/Upcast
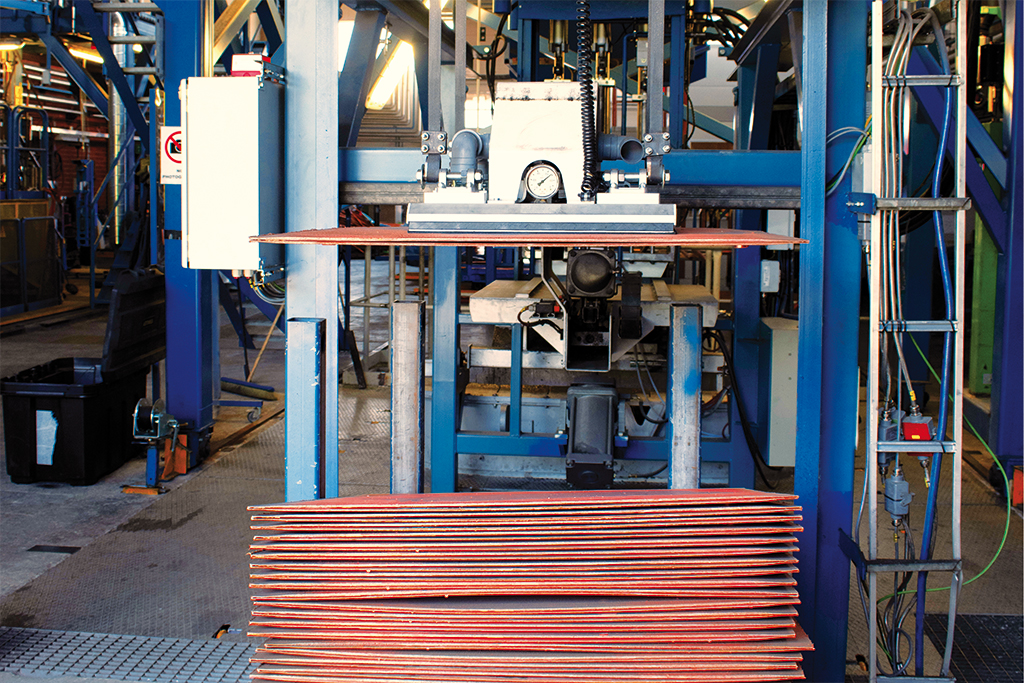
The UPCAST® continuous casting lines are of modular construction and, thus, upgradeable to meet the requirements of modern technology. The production demands vary based on new products or larger capacity requirements and with the upgrades it is possible to answer these needs. The most common upgrades are those related to the automation.
– For example, the upgrades of the servo motors, which keep the casting process running, are our standard products. Technology ages as automation develops and there are no longer compatible parts available, but, luckily, the servo system can be updated to a new and modern system, Senior Sales Manager Tuomas Rajaviita says.
There is also the newest technology available for the steering of the casting lines.
– Old computers will not live forever. At offices we update our computers on a regular basis, and the same should also be done with the control PCs running the monitoring system.
With the inductor upgrade, the furnace becomes more efficient, energy friendly and remarkably longer lasting.
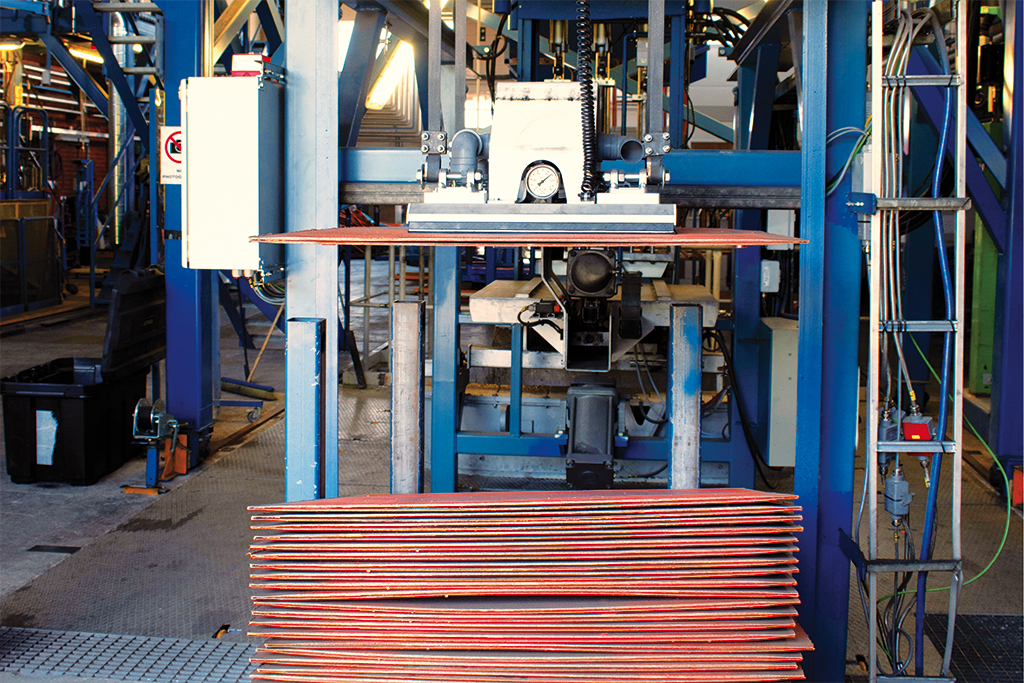
In addition to savings, the upgrades increase the convenience and safety of the operation.
Energy efficiency and savings with upgrades
One remarkable renewal for the line is the inductor upgrade for the furnace where the old single loop inductor is replaced by an efficient and modern double loop inductor.
– With the inductor upgrade, the furnace becomes more efficient, energy friendly and remarkably longer lasting. The production costs of the customer will decrease, since the electricity consumption is smaller and the time between the required maintenance becomes longer.
UPCAST Oy has already for quite some time supplied a new PreCast shape furnace lining, of which the installation time is remarkably shorter. In comparison with bricklaying, we are talking about weeks. It is a great difference for the customer when we think about closing the production for several weeks, whereas the PreCast lining can be carried out within less than a week.
To ease the charging of the copper cathodes, the company has developed a new type of suction plate. In the past, the cathodes were lifted with a traditional suction cup and, in case there was an unevenness or holes on the cathode, the grip was sometimes not tight enough to hold its weight.
– The new suction plate that we have developed will stick to and hold almost anything and, thus, it can also lift cathodes of a somewhat worse quality.
There are customers in the world who are still casting with UPCAST® lines supplied in the 1980´s and are still running thanks to upgrades over the years. In addition to savings, the upgrades increase the convenience and safety of the operation.
– We are continuously improving and developing the products and the process and searching for new components to replace the ones that are no longer available, We also need to carefully follow the safety requirements and regulations and take any changes into account in our development work, Rajaviita says.
Tuomas Rajaviita Senior Sales Manager
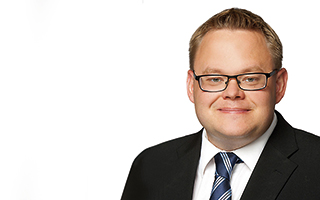