Upgrade of PILOT test facility opens up new opportunities
There is always something going on at the UPCAST® Pilot test facility, with its renewals and improvements. Top modern casting lines make it possible to test and develop the equipment, products and processes better than ever before.
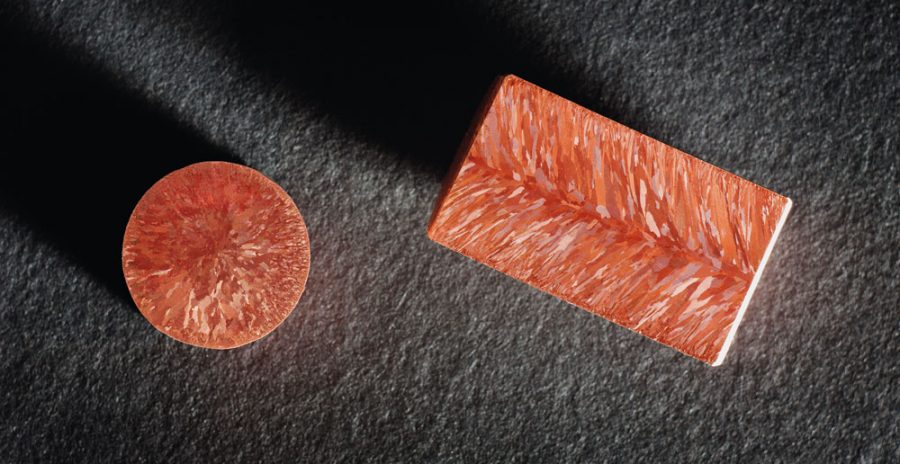
In the UPCAST® Pilot hall the tests are carried out on two casting lines: one is equipped with a 6 tonne melting/casting furnace with 400kW channel inductor, and the other one is a 3 tonne crucible induction furnace. The first one is a hybrid line where almost any size of rod and tube can be cast, with normal sizes for the rod being between Ø8–30 mm and for tube Ø20–60mm. It is also possible to cast various profiles with UPCAST® process, and the recent flat bar tests have been very successful.
For the no. 1 line there was an upgrade at the turn of the year.
– We replaced the old power control with a modern stepless TIV power control with IGBT transistors. This way the power control is more flexible, so the temperature control becomes more accurate, which is very important for testing. Energy savings come as a bonus with the new system. We also renewed the cooling water system, which ensures a constant water temperature and minimum water consumption. To move the heat energy away in the secondary circuit, we use water from the river, but with these changes we have also minimised its consumption, says R&D and Engineering Manager Markku Koivisto.
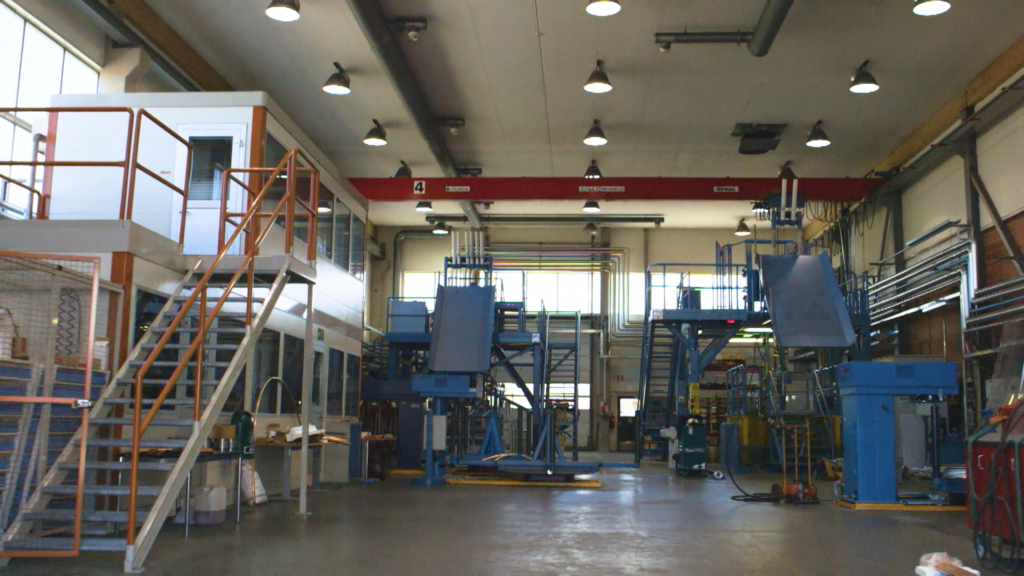
The second line was commissioned about two years ago, thus far with very positive results and experiences. This line is specifically reserved for the testing of various alloys.
– The advantage of the crucible furnace is the easy restart after emptying and cleaning the previous alloy. Naturally this line is also equipped with the stepless TIV control and accurate cooling water system, thus minimising consumption, Markku continues.
For every new alloy, we want to make certain through testing that with the UPCAST® process the alloy in question can be produced into high quality cast products that meet customer requirements in terms of their high quality raw material.
Most important alloys under testing are CuMg0.5 and ZnAl15
The most important alloys under testing are currently CuMg0.5, ZnAl15 and various brass alloys. CuMg has excellent strength and conductivity characteristics, which create several opportunities for its applications, such as contact wires for high speed trains, and low current and signal cables for the automotive industry.
– The electricity transfer system, which is in contact with the contact cables on a train´s roof, causes mechanical oscillation in the cables creating waves, which have to move faster than the train itself in order to avoid the destructive standing wave in the cables. That is why it is essential for the contact cable to be tightened into a high pull tension above the tracks to reach the maximum speed. This requires strength.
Modern cars have complicated systems requiring more electric cables but at the same time weight increase has to be prevented. Again, the solution can be found in CuMg. Due to smaller cross sections, less material is needed, so the weight control of the car is effective.
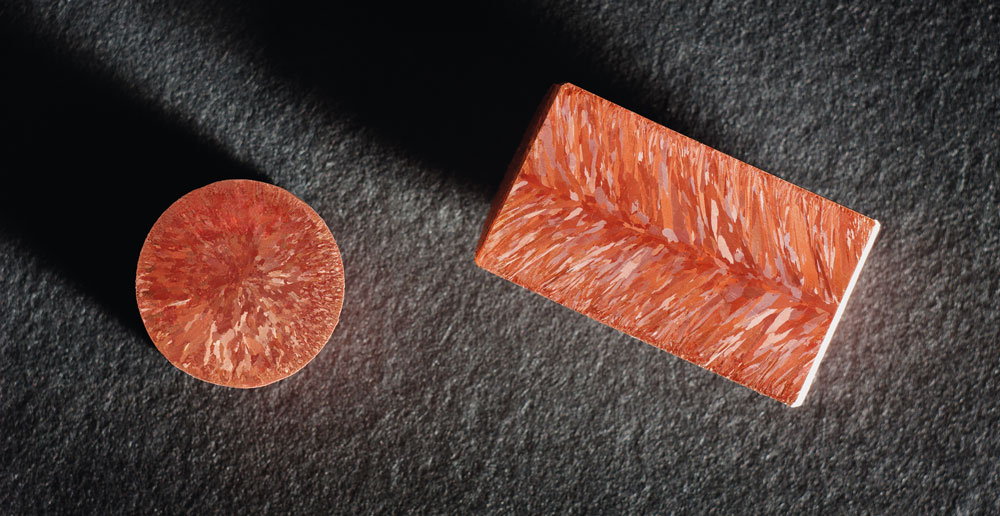
Koivisto reminds us that, as he promised in the previous UPCAST Review, we will find out more about UPCAST® CuMg products at the end of the year.
– We have already cast the biggest diameters of CuMg0.5, the rod has been processed, and the finished wire satisfies the requirements of EN 50149 standard. In addition, we have already produced an Ø8mm CuMg0.5 cast rod, which has been further processed into thin wires suitable for the automotive industry. With the cast diameter of Ø8mm, the process to the finished product is shorter and thus also more cost effective.
A big advantage is that with the hot press you can produce products with only specific lengths, whereas with UPCAST® technology we can cast rods into coils in exactly the optimised amounts for the customer needs.
New technology for ZnAl alloy
ZnAl alloy is used in the arc and flame spraying process for corrosion protection. The very fine ZnAl wire is led into the spraying gun where it melts and is then sprayed onto a steel surface, forming a film that protects the steel from corrosion.
The technology for casting ZnAl mix into a cast rod is new.
– We were contacted by a customer who wanted to cast the ZnAl with UPCAST® technology. We then developed the process together so that we could cast a Ø12mm rod, which the customer can further process into smaller diameters, all the way down to Ø1.2mm. The test batches were done some time ago and we will cast more so that we can have enough material to work together at the customer end to make the technique work in their process, says R&D Engineer Juho Kalliokoski.
There are remarkable benefits in the new technique.
– Compared to the traditional production method of this alloy, the investment cost is clearly lower. In addition, a big advantage is that with the hot press you can produce products with only specific lengths, whereas with UPCAST® technology we can cast rods into coils in exactly the optimised amounts for the customer needs, Juho continues.
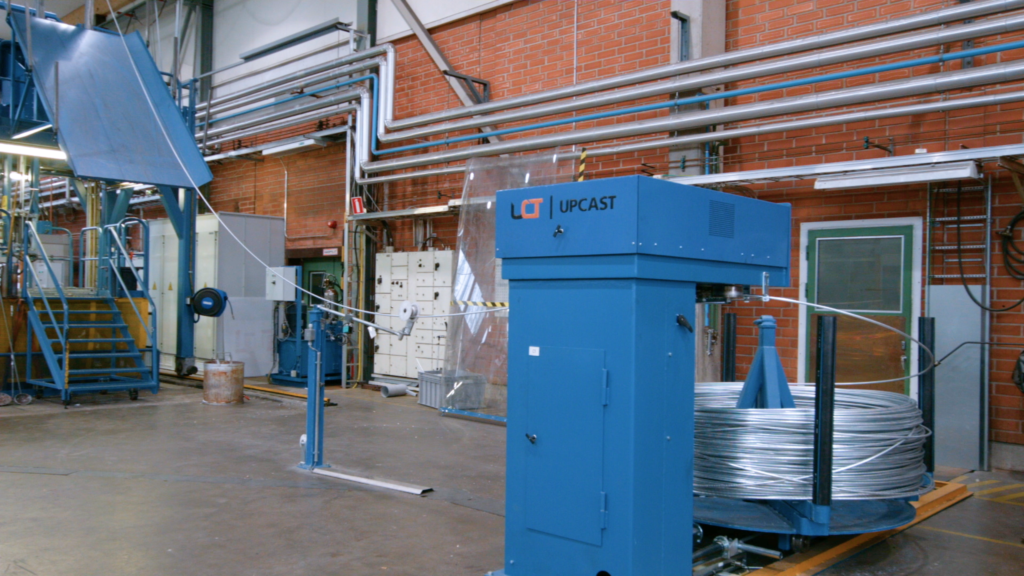
In the future, the focus of the R&D will be on the alloys, while at the same time not forgetting the further development of OF and DHP products. We will also see the PILOT casting of e.g. CuSn and CuNi, the latter one offering good durability in sea water. CuNi tubes have already been cast and tested with excellent results.
For every new alloy, we want to make certain through testing that with the UPCAST® process the alloy in question can be produced into high quality cast products that meet customer requirements in terms of their high quality raw material. Based on our wide and long-term cooperation network, we can test the products under development all the way to their final dimensions, states Markku, in conclusion.